From Retail to Manufacturing: Tailored Inventory and Payroll Strategies for Success
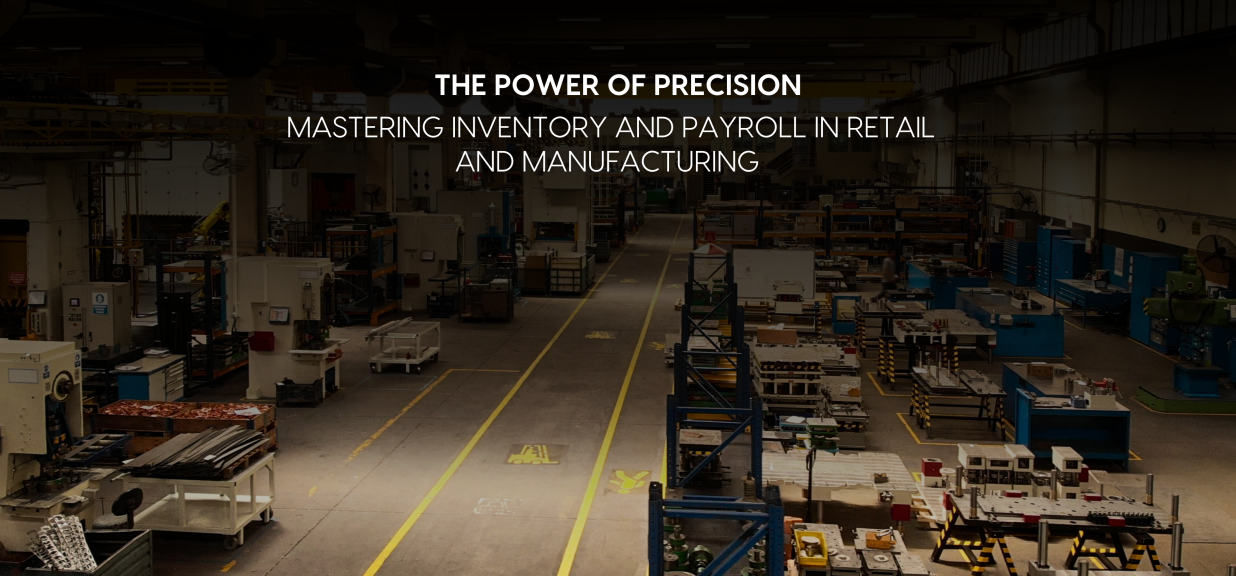
Did you know that nearly 43% of retail businesses cite inventory management as their top challenge? According to the National Retail Federation (NRF), effective inventory control remains one of the biggest pain points for retailers, especially in an era where demand can be unpredictable.
On the flip side, manufacturers face unique obstacles, such as material shortages and complex payroll calculations. A survey from the Manufacturing Institute reveals that around 50% of manufacturing firms struggle with finding the right balance between labor costs and production efficiency, highlighting the ongoing challenge of managing resources effectively.
In this blog, we explore how businesses in both sectors can optimize their inventory management and payroll systems, offering data-driven insights, real-life examples, and strategies for success.
Understanding the Differences Between Retail and Manufacturing Operations
Key Characteristics of Retail Businesses
Retail businesses operate in a fast-paced environment where stock turnover is rapid and consumer preferences fluctuate frequently.
In fact, a recent survey revealed that 61% of retail businesses face challenges related to unpredictable demand, emphasizing the importance of having a responsive inventory system. This highlights the need for retailers to enhance their forecasting strategies, ensuring they can adjust quickly to market shifts and consumer behavior. Retailers must constantly track inventory, manage seasonal spikes, and ensure smooth customer-facing operations, which all require tailored strategies. Efficient inventory systems like point-of-sale (POS) and RFID technology help retailers keep stock levels accurate and customers satisfied.
Key Characteristics of Manufacturing Businesses
Unlike retail, manufacturing is driven by production schedules, raw material tracking, and long-term inventory planning. Manufacturers often deal with batch production and face challenges such as coordinating materials, managing suppliers, and ensuring that the right components are available at the right time. According to the Manufacturing Institute, 44% of manufacturers cite supply chain disruptions as a top issue.
Tailored Inventory Strategies for Retail
Real-Time Inventory Tracking
For retailers, real-time inventory tracking is not just a convenience—it’s a necessity. A recent survey by the National Retail Federation found that retailers using automated inventory systems saw a 10% reduction in stockouts and a 15% decrease in excess inventory. Technologies such as RFID and barcode scanners allow for accurate stock counts in real-time, ensuring businesses know exactly what’s on their shelves at any given moment.
Different business types require tailored approaches to inventory and payroll management based on their unique operational needs. For instance, jewelry stores, as a specialized retail business, face additional challenges when it comes to inventory management and payroll. The value of their products, such as gemstones, metals, and intricate custom designs, requires accurate tracking to prevent theft and ensure inventory levels align with customer demand. In this context, using software solutions that cater to the jewelry industry's specific needs can provide significant benefits. Solutions like CaratIQ integrate inventory tracking, sales data, and payroll management into a unified system, helping jewelry stores streamline operations and improve both efficiency and profitability.
Tailored Inventory Strategies for Manufacturing
Raw Material and Component Inventory Management
In manufacturing, managing raw materials and components is the foundation of the production process. If materials are out of stock or not delivered on time, production can grind to a halt. Companies like Toyota use Just-in-Time (JIT) inventory systems to avoid overstocking while ensuring timely deliveries from suppliers. JIT allows manufacturers to reduce holding costs and minimize waste, but it requires precise coordination and communication with suppliers to ensure that the materials are available when needed.
Production Scheduling and MRP
Production scheduling in manufacturing must be tightly linked to inventory management to ensure that materials are available when needed and production runs smoothly. Material Requirements Planning (MRP) systems integrate inventory management with production schedules to ensure alignment. Companies like General Electric use MRP to manage production deadlines and ensure they have the right materials for each job. Businesses that integrate MRP with their inventory systems report a 30% increase in production efficiency.
Payroll Strategies for Retail
Employee Scheduling and Wage Management
Retailers often deal with fluctuating customer traffic, requiring flexible scheduling systems that adapt to shifts in demand. This is especially true for businesses that operate on a seasonal or part-time basis. Advanced payroll systems like Neeyamo help retailers create schedules based on sales data, ensuring labor costs are kept in check while meeting demand.
Compliance with Labor Laws and Regulations
With constantly changing labor laws, retail businesses need a payroll system that ensures compliance. For example, in the US, many states have passed laws requiring paid sick leave for retail workers, and failure to comply can lead to significant penalties.
Tips, Commissions, and Incentives
Retail businesses often have employees who earn tips or commissions, which can complicate payroll calculations. Companies like Starbucks use sophisticated payroll systems to calculate tips and commission payments, ensuring accurate and timely payouts to employees. Research by the U.S. Department of Labor shows that businesses with automated tip and commission tracking reduce errors by up to 20%.
Payroll Strategies for Manufacturing
Managing Shift Workers and Overtime
Manufacturing operations often rely on shift work, overtime, and fluctuating schedules, making payroll calculations more complex. A survey from the American Payroll Association found that 56% of manufacturing companies report errors in overtime calculations. Adopting automated systems like Kronos Workforce Ready ensures that shift differentials, overtime, and holiday pay are calculated accurately and efficiently, avoiding costly errors.
Integrating Technology for Both Retail and Manufacturing
Automation in Inventory Management
Both retail and manufacturing businesses benefit from automated inventory systems. By integrating technologies such as RFID and cloud-based tracking systems, businesses can minimize errors and reduce time spent on manual inventory checks. A study by Zebra Technologies found that 70% of businesses that adopted automation saw a 20% improvement in inventory accuracy.
Embracing Technology for Business Growth
From retail to manufacturing, the need for tailored inventory and payroll strategies is clear. While both industries share core operational challenges, the unique characteristics of each require distinct approaches to inventory and payroll management. By embracing technology, leveraging automation, and staying responsive to the needs of the business, companies in both sectors can streamline their processes, reduce costs, and ultimately drive growth. The key is to never underestimate the power of a well-crafted, industry-specific strategy—because success is often in the details.
Latest Resources
Stay informed with latest updates
If you're curious and have a thirst for knowledge pertaining to the HR, payroll, and EOR universe, don't miss out on subscribing to our resources.